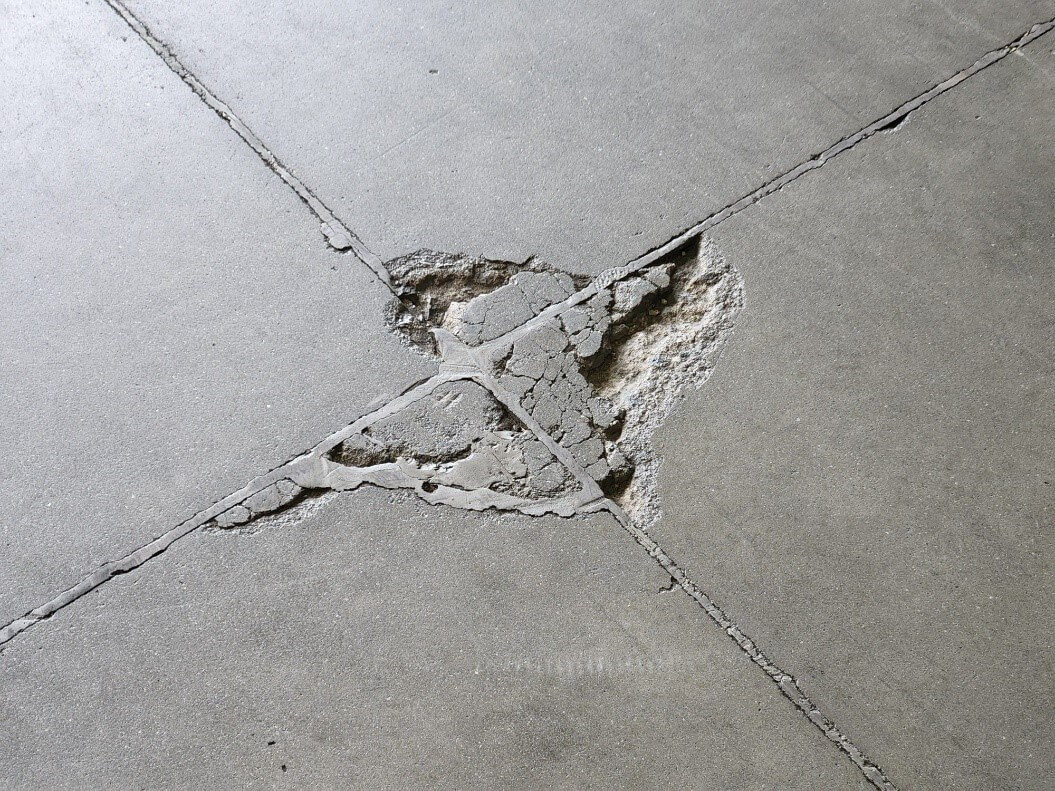
OUR SERVICES
[zipcoderedirect]
Concrete Warehouse
Floor Joint Repair
A Vital Investment for Long-Term Durability and Forklift Safety
In the realm of industrial infrastructure, warehouse floors play a pivotal role in ensuring the smooth functioning of operations. With constant traffic from material handling and heavy machinery, forklifts, and high storage loads, these concrete floors are subject to wear and tear, especially at the joints. Over time, these joints can deteriorate, leading to safety hazards, operational inefficiencies, and increased maintenance costs.
The process of concrete warehouse floor joint rebuilds has emerged as a crucial investment for companies seeking to ensure the durability and efficiency of their warehouse facilities. If you are searching for commercial concrete floor repair near me, Concrete Chiropractor® offers solutions to these concrete floor failures throughout New Jersey and Eastern PA.
Understanding the Significance of Concrete Warehouse Floor Joints:
Concrete warehouse floor joints are designed to absorb the stress and movement of heavy equipment, temperature fluctuations, and natural settling of the building. However, constant wear and tear can lead to joint deterioration, causing various issues such as:
- 1
Uneven surfaces: Deteriorated joints can result in uneven surfaces, creating potential hazards for the operations of pallet trucks, pallet jacks, machinery, and personnel, leading to accidents and operational disruptions.
- 2
Dust and debris accumulation: Damaged joints can facilitate the accumulation of dust and debris, which not only compromises the cleanliness of the warehouse but can also affect the performance of equipment and machinery.
- 3
Increased maintenance costs: Neglecting deteriorating joints can result in more extensive damage over time, leading to costly repairs and downtime that can impact the bottom line.
The Rebuilding Process:
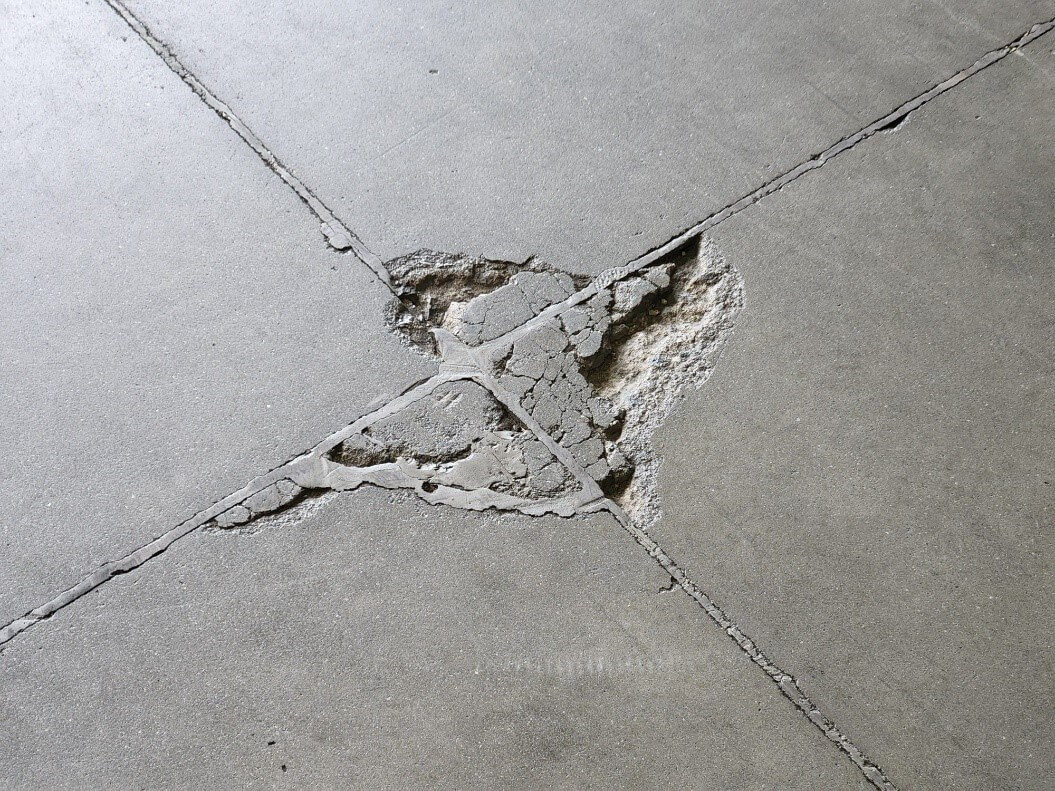
Concrete warehouse floor joint rebuilds involve several crucial steps to ensure the restoration of the floor's structural integrity and functionality. The process typically includes the following steps:
- 1
Evaluation and planning: A professional, comprehensive assessment of the condition of the floor joints is conducted to determine the extent of damage and the appropriate rebuilding strategy. This evaluation helps in devising a customized plan to address specific issues and requirements.
- 2
Removal of damaged concrete: The damaged concrete and debris are carefully removed from the joints using specialized equipment, ensuring minimal disruption to the surrounding areas and operations.
- 3
Preparation of the surface: The exposed joints are thoroughly cleaned and prepared to create a strong bond with the new concrete, enhancing the longevity and durability of the rebuilt joints.
- 4
Application of new concrete floor repair mortars: High-quality epoxy mortars are often applied to the joints, incorporating advanced techniques to ensure a seamless and durable finish that can withstand heavy loads and constant traffic.
- 5
Finishing touches: After the new concrete is applied, finishing touches such as concrete floor grinding are implemented to smoothen the surface and ensure uniformity, creating a seamless transition between the old and new concrete.
Benefits of Concrete Warehouse Floor Joint Rebuilds:
Investing in concrete warehouse floor joint rebuilds offers numerous benefits, including:
- 1
Enhanced safety: Rebuilt joints contribute to a smoother and more even surface, minimizing the risk of accidents and injuries for both personnel and equipment, such as electric pallet jacks.
- 2
Improved efficiency: A well-maintained warehouse floor ensures the seamless movement of machinery, optimizing operational efficiency and minimizing downtime. Also, industrial concrete floor repairs that are minimal can be repaired in less time than those with severe damage.
- 3
Long-term cost savings: By addressing joint deterioration promptly, companies can avoid extensive damage and costly repairs in the future, leading to significant long-term cost savings.
- 4
Extended lifespan: Rebuilt joints enhance the structural integrity of the warehouse floor, extending its lifespan and reducing the need for frequent repairs and maintenance.
Conclusion:
Concrete warehouse floor joint rebuilds are a vital investment for companies seeking to maintain the functionality and longevity of their warehouse facilities. By addressing joint deterioration promptly and effectively, organizations can ensure a safer working environment, improved operational efficiency, and long-term cost savings.
Embracing this proactive approach not only protects the infrastructure but also fosters a conducive environment for sustainable business growth and development. If you are a warehouse or facility operations manager in the NJ or Eastern Pennsylvania area, call Concrete Chiropractor® for a professional evaluation of your concrete floor repairs.